Purity and certifications
Product purity is, along with excellent design and functionality of products, an important and solid foundation that enables customers to generate reliable, reproducible and trustworthy results. BIOplastics products are fully traceable and frequently tested during production. BIOplastics products comply with the highest standards and requirements. Polypropylenes are medical grade and fully incoming quality controlled, prior to use in our proprietary blending methodology. All injection molding process parameters, QC tests and packaging are monitored, logged and fully traceable. If required, BIOplastics will provide batch certificates as well as individual certificates.
Certificate of Analysis (COA)
All BIOplastics products are extensively process qualitycontrolled and tested. Our QC-laboratory does the final testing prior release to the warehouse. A Certificate of Analysis can be requested at the BIOplastics website. Each request for COA will be re-traced in our fully traceable system prior to COA release.
Traceability of products
BIOplastics has a fully compatible traceable system in place. This means that each bag can be traced from the incoming raw material through production to whom the product was sold. Traceability is 100% and based on more than 80 parameters.
Cleanroom, “no hands on” manufacturing
BIOplastics products are molded and automatically collected, inspected, quality controlledand packaged in a Class 100,000 cleanroom environment. Manufacturing, packaging, in process and final release QC, operate as independent entities, each with independent responsibilities. Appropriate body protection, including masks and gloves are mandatory for all departments.
ISO9001
BIOplastics’ company procedures are similar to ISO9001 and GMP procedures. Although we formally do not
have to carry an ISO9001 stamp we are scheduled to have an ISO9001 accreditation shortly.
Yellow bags, why?
Although BIOplastics manufactures all its injection molding products, we do not manufacture the bags where the products are packed into. They are manufactured by an external blow molding company. Although the bags are guaranteed clean we still take extra precautions. We therefore sterilize all packaging material, in particular “zip lock” bags by means of cobalt
60. Cobalt
60 irradiated plastics may lead to a slightly more brittle bag as well as slightly yellow discoloration. (may vary based on amount of radiation and batch of bags)
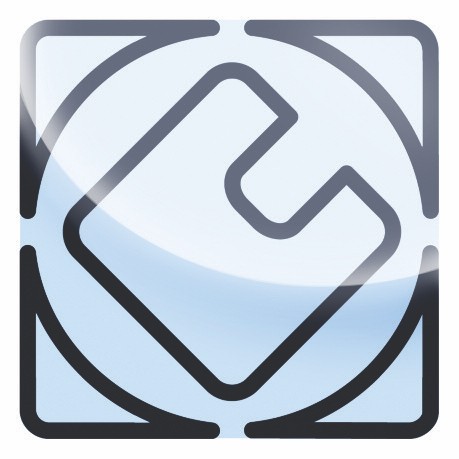
Product is autoclavable when you see this icon
Autoclave when, how and why?
All BIOplastics products are autoclavable except the easy closure screw caps. Autoclaving instructions:
15 minutes at 121°C and 2 bar pressure. A lot people confuse sterile products with DNa(se), RNa(se), Protein and DNA free products. BIOplastics (q)PCR products are manufactured free of any detectable levels of DNa(se), RNa(se), proteins and DNA. So the products do NOT REQUIRE any additional treatment.
The AUTOCLAVING process DOES NOT REMOVE any DNA, RNA or proteins. It does however breakdown larger molecules and “kill” living organisms. So a sterile product is not necessarily a DNA, RNA free product whereas a DNa(se), RNa(se), Protein and DNA free product can by definition not be categorized as sterile.
Bottom line for all BIOplastics products in general: Use them as they come!
60Co irradiation exposed sticker as sterility indicator
What is sterility?
A sterile product is a product which is free of any living micro-organisms. Sterilization of BIOplastics products is accomplished by means of cobalt
60 irradiation. Irradiated products age faster than non-irradiated products; they are less flexible and break more easily, because cobalt
60 irradiation slightly changes the characteristics of the polymer material. Autoclaving the product yourself is a more gentle process, but when done several times it will also harden the polymer. One could argue whether it is necessary to autoclave or irradiate BIOplastics (q)PCR disposables at all, since our products are produced under cleanroom and “no-hands-on” conditions.
See also autoclave when, how and why? (Page 18).
What is DNa(se), RNa(se) and pyrogen-free?
Producing products under strict cleanroom and “no-hands-on” conditions ensures the absence of DNA, RNA, and their breakdown enzymes. A sterile product is not necessarily DNA(se), RNA(se) and pyrogen-free.
Only regular testing during and after the production process guarantees a DNA(se), RNA(se) and pyrogen-free product. You can recognize the DNA(se), RNA(se) and pyrogen-free plastics in this catalog when you see the “Thumbs-Up” icon.
Human DNA and ATP absence?
Manufacturing products under strict clean and “no hands-on” conditions, as well as regular testing during and after the production process, ensures the absence of human DNA and ATP.
What is metal-free?
The absence of metals in polymer products like tips and tubes is essential for laboratory use, as metals can interfere in (q)PCR and other reactions with ions as Mg2+. BIOplastics tips and tubes are made of PP (Polypropylene) of the highest medical grade quality available and guaranteed metal free.
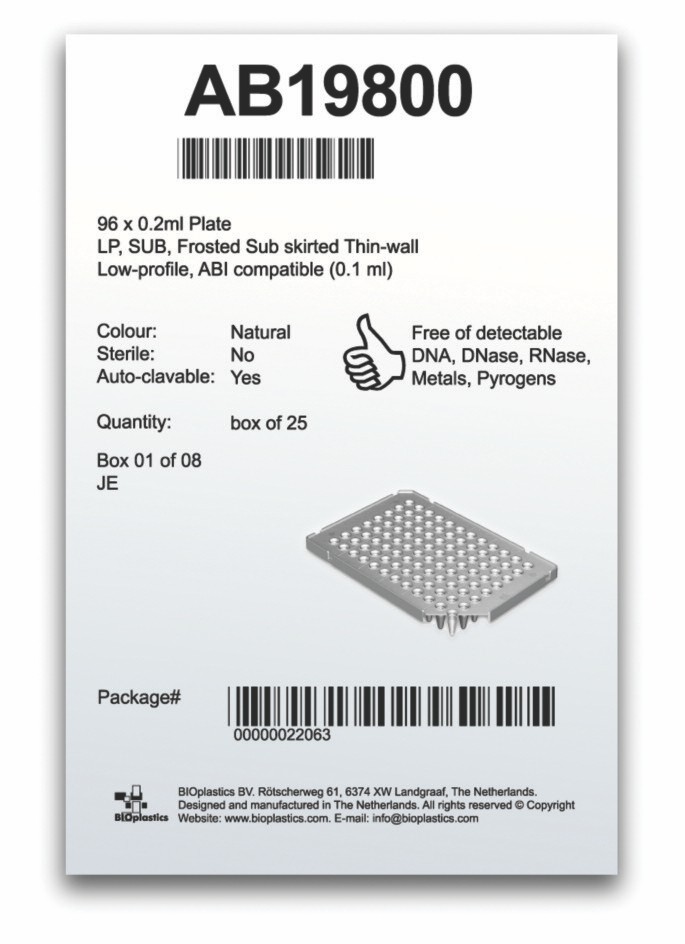
Example of product package label with individual bag ID
Why we do not work with lot#, but with individual trace ID# instead
Most companies work with so called Lot ID#(lot number). We at BIOplastics do not use the “lot ID” categorizations since raw material and time is involved in its definitions. Since we prefer to have more exact and precise data, we have narrowed the time factor down to a maximum range of 4 hours. It is for that reason that we use individual bag IDs which enable us to trace and isolate products to a manufacturing and packaging time frame of 4 hours maximum. Ultimately this is beneficial for you as a customer as it is for us.
While this has not yet occurred, in any particular case it would enable us to recall products to a production time of 4 hours. Since we can trace to whom we sold individual bags, we would be able to precisely isolate products without interfering or disturbing non involved customers.
Complaints
BIOplastics is proud that the number of product complaints is very low. Furthermore 97% of claims ever received could be traced back to a user related issue. Let’s be clear: We at BIOplastics aim for 100% product satisfaction. We feel obligated to achieve this goal and have a team of application specialists available to help and investigate. Should you have a complaint, then we will ask you to fill out a complaint form including details of your experiments, as well as returning the products in question if possible. In all cases we will counter investigate and report our findings and recommendations back to you. If a claim is granted by our specialist teams we will replace the product free of charge. If a claim is not granted we will contact you and provide you with details on how to solve your problem. We believe this to be a fair, functional, and "no nonsense" policy.